Comprehending Welding WPS: Comprehensive Overview for Welders
Comprehending Welding WPS: Comprehensive Overview for Welders
Blog Article
Grasping Welding WPS Criteria: Finest Practices and Techniques for Top Quality Welds
In the world of welding, grasping Welding Procedure Requirements (WPS) requirements is a vital component that straight affects the top quality and stability of welds. Complying with these standards ensures uniformity and integrity in welding end results. Nevertheless, accomplishing excellence in welds exceeds merely recognizing the requirements; it involves applying best techniques and strategies that raise the craft to a level of precision and skill that sets apart the average from the extraordinary. As we browse via the details of welding WPS criteria, discovering vital understandings and approaches for accomplishing top-tier welds will certainly be paramount for welders looking for to master their craft and create welds that stand the test of time.
Understanding Welding WPS Specifications

Assessors count on WPS paperwork to verify that welding procedures are being complied with correctly and that the resulting welds are of high quality. Designers utilize WPS standards to design welding treatments that ensure the durability and integrity of welded structures.
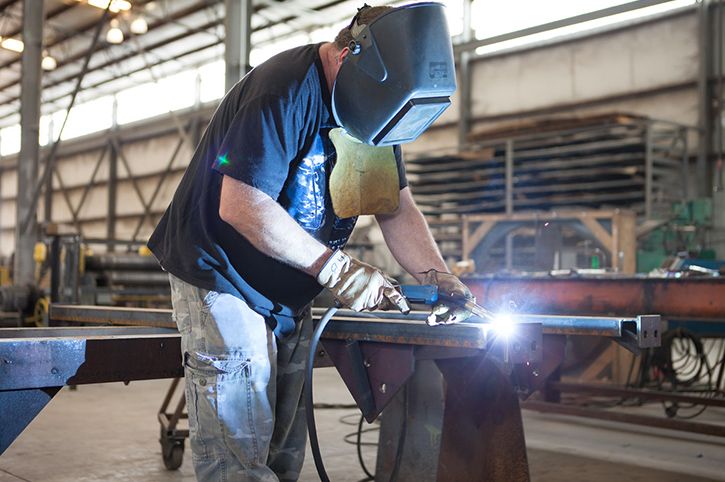

Necessary Tools for High Quality Welds
Grasping welding WPS standards is vital for welders to effectively utilize the crucial devices needed for creating high quality welds. Among one of the most important tools for top quality welds is a welding equipment. The kind of welding equipment required depends upon the welding process being made use of, such as MIG, TIG, or stick welding. Welding headgears are likewise essential to protect the welder's eyes and face from triggers, heat, and UV radiation. In addition, welding handwear covers made from heat-resistant and durable products secure the hands from burns and injuries. Clamps and magnets aid hold the work surfaces together securely throughout the welding procedure, ensuring precise and precise welds. Cord brushes and cracking hammers are vital for cleaning the weld joint before and after welding to eliminate any type of contaminations that might influence the high quality of the weld. Last but not least, a gauging tape and angle mill work tools for making sure correct positioning and preparing the workpieces for welding.
Key Methods for Welding Success
To attain welding success, one have to understand the vital strategies vital for producing top quality welds. Maintaining a stable hand and a stable welding placement throughout the process is key to attaining precision and uniformity in the welds. By grasping these key strategies, welders can raise the quality of their job and accomplish welding success.
Ensuring Conformity With WPS Specifications

In addition, keeping detailed documents of welding parameters, equipment calibration, and inspection outcomes is vital for demonstrating compliance with WPS criteria. By carefully adhering to WPS standards, welders can ensure that their work satisfies the needed high quality levels and contributes to the general success of the welding job.
Troubleshooting Common Welding Issues
When faced with usual welding problems, determining the origin reason is critical for effective troubleshooting. One widespread issue is the presence of porosity in welds, commonly brought on by contaminants such as dampness, oil, or rust. To resolve this, guaranteeing appropriate cleaning of the base steel before welding and making use of the appropriate shielding gas can substantially lower porosity. Another concern frequently run into is absence of combination, where the weld stops working to effectively bond with the base product. This can originate from poor warmth input or improper welding technique. Adjusting criteria such as voltage, wire feed rate, or take a trip rate can aid boost blend. Additionally, distortion, splitting, and spatter are common welding challenges that can be mitigated through correct joint preparation, constant warmth control, and picking the proper welding consumables. By completely recognizing informative post these common welding problems and their root causes, welders can successfully fix issues and achieve top notch welds.
Final Thought
To conclude, understanding welding WPS standards requires a comprehensive understanding of the guidelines, utilizing important devices, and applying vital strategies for effective welds. Ensuring conformity with WPS standards is essential for producing quality welds and staying clear of typical welding problems. By complying with best practices and methods, welders can accomplish consistent and dependable outcomes in their welding jobs.
In the realm of welding, understanding Welding Treatment Specification (WPS) requirements is a critical component that straight affects the quality and stability of welds.When delving into the realm of welding methods, an important aspect to comprehend is the relevance and details of Welding Treatment Specification (WPS) standards. WPS requirements give a detailed guideline for welding operations, link making sure uniformity, top quality, and safety in the welding process. The type of welding device required depends on the welding procedure being made use of, such as MIG, TIG, or stick welding.Attaining welding success website link via the proficiency of crucial methods necessitates an extensive understanding and adherence to Welding Treatment Spec (WPS) requirements.
Report this page